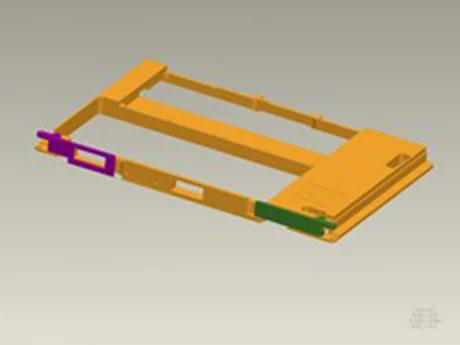

Customer: Leading UK tier 1 Avionics Company
Background: The customer had an initial design of a machined investment casting which had a number of problems.
The customer approached RET due to a previous, highly successful programme on a wide body civil airliner. RET was invited to work on the project with a view to breaking the casting design down into a mosaic of machined parts to achieve the mechanical specifications, replacing a cachined casting with a construction from machined panels. This represented a new challenge as the environmental and performance requirements for a front-line fighter are well above the previous civil project where RET collaborated with the customer but both design teams were sure they could meet and exceed the operating requirements.
The customer and the Eurofighter Consortium approved RET’s proposal so an initial prototype was manufactured. This was put through preproduction build and put into initial qualification trials. The unit passed all tests. Further refinement was carried out but no further pre-production assemblies were needed, as the modular construction meant that the final manufacturing configuration could be altered until the very last minute.
The benefits shown by RET during design and test were:-
a) Component much more rigid than previous cast version.
b) Eliminated high reject rates of previous cast design.
c) RET machining process in control, previous machining of the cast version was far from so.
d) Production rates brought in-line to support the Typhoon programme over the forthcoming decade; previously readiness reviews showed the previous manufacturing process was incapable of doing so which would have been unacceptable.
e) Performance under vibration brought into mechanical design specifications, including vibration when the pilot is firing the aircraft weapons.
f) Overall weight for the mechanics was reduced from the cast version.
g) EMC/EMI and RFI requirements were exceeded where the cast version had been leaking around covers and interfaces.
Following the initial prototype, the unit went straight into volume production and over 700 units have been successfully delivered to date.